Machining plastic, composites, and metals to precise project specifications is vital to success and unlocks many applications across several industries. Precision machining allows companies to repeatedly and reliably produce intricate components with tight tolerances. Let’s unpack precision machining and its benefits.
What is Precision Machining?
Precision machining is a specific manufacturing process capable of accurately fabricating complex components with incredibly fine tolerances, as low as +/—0.005 inches. It incorporates the use of CNC (Computer Numerical Control) machinery, featuring automated processes using tools to shape, cut, and drill materials to high-quality finishes and precise dimensions.
Achieving manufacturing results with micron-level precise manufacturing requires advanced CNC machines such as lathes, mills, and grinders capable of positioning cutting implements along several axes using coordinate-driven computer program commands.
Precision CNC machining provides high-speed, ultra-sharp cutting tailored to specific materials, achieving excellent form accuracy and surface finish. Components receive fine-tuning until they satisfy quality and dimensional specifications.
Precision machining offers unparalleled accuracy and repeatability that are unattainable through manual processes. This makes it ideal for mass production of dimensionally identical parts. Precision machining serves several industries, from optics and aerospace to electronic, automotive, and medical.
Precision Machining – A Step-by-Step View of the Process
Step #1 – CAD Design
A design specialist creates a 3D computer model of the desired component.
Step #2 – CAM Programming
The CAD design converts to a CAM (Computer Aided Manufacturing) model, which turns it into numeric code and provides manufacturing instructions to the CNC machine.
Step #3 – Fixturing
The manufacturer selects the correct material for the project and fixes the workpiece using vices, clamps, or adhesive.
Step #4 – Tool Setup
The CNC machinist initiates the CAM program and executes the sequence to direct machine movements, including a selection of cutting tools, spindle rotation speed, cutting depth, and feed rate.
Step #5 – Machining
The machine manipulates the tool according to the CAM program instructions, creating high-precision components. It finishes, polishes, deburrs, coats, and heat treats the final workpiece to project requirements.
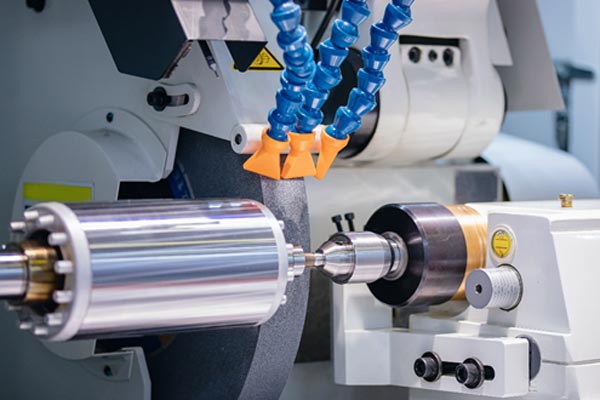
CNC milling
Understanding The Types of Precision Machining
CNC Machining
Computer numerical control (CNC) machines involve turning, milling, drilling, and grinding tools programmed to initiate CAM software commands input by a qualified machinist. The program directs machine movements along multiple axes to bore, cut, and shape components. The program controls factors like spindle speeds, feed rates, cutting depth, and more.
Multi-Axis CNC Machining
These machines come in models offering multi-axis CNC machining on up to five axes. They enhance manufacturing flexibility in shaping complex curved geometries and 3D contours in a single setup. 5-axis milling is the peak of the technology, offering manipulation of the workpiece along X, Y, and Z axes while rotating and tilting the workpiece.
CNC Drilling
These machines drill holes accurately, offering extreme precision that’s unattainable through manual drilling processes. The machine can spot, countersink, bore, tap, and ream workpieces via programmable CAM instructions.
CNC Turning
The CNC lathe rotates a workpiece against a motionless cutting tool to machine contours, diameters, faces, and grooves. CNC turning can handle tapered and straight diameters and eccentric contours via CAM programming. The machine offers versatile production qualities with a single setup.
Swiss Machining
Aka, “Swiss turning,” this specialized CNC method incorporates automatic lathe technology. The lathes feature a moving guide bush and headstock, enabling support for centralized workpieces while completing cutting actions along several axes. This functionality enhances stability in high-precision small-diameter machining applications. Swiss machines provide faster component cycle times by enabling simultaneous backside and frontside machining.
Electrical Discharge Machining (EDM)
EDM machining technology involves the application of electrical spark erosion, which vaporizes conductive materials. It’s an automated alternative to conventional grinding or cutting processes. EDM utilizes no cutting forces but maintains high accuracy in die making, cavity sinking, and machining applications at the micro level to precise tolerances under 0.001-inch. It’s a slower process compared to other CNC techniques. However, wire and sinker EDM processes use exotic alloys to meet unique requirements for fragile tooling and micro-sized parts.
Wrapping Up – Materials Used in Precision Machining
Plastics
Polymers and plastic materials such as acrylic, PVC, PEEK, and nylon have excellent thermal and electrical properties. While many manufacturers choose injection molding as a manufacturing technique for these materials, CNC machining offers the addition of precision details to components.
Metals
Stainless steel, aluminum, nickel alloys, and titanium are common materials used in component manufacturing with CNC machining applications. They offer durability and strength to enable tight tolerances in CNC manufacturing processes. These metals also allow for heat treatment to enhance component hardness.
Glass
Glass provides exceptional optical clarity and heat, chemical, and electrical resistance. CNC machining processes like drilling, milling, and turning enable the production of precision parts like prisms, lenses, and ceramic components.
Composites
The combination of two base materials creates a composite with beneficial properties. Carbon fiber reinforced polymers (CFRPs) are a good example, offering exceptional strength-to-weight ratios.
Ceramics
Technical ceramics from silicon carbide, aluminum oxide, silicon nitride, or zirconium oxide offer heat resistance and exceptional hardness. However, the brittle nature of these materials limits the geometry of parts to simple forms.
Natural Materials
Waxes, wood, foam, and rubber are suitable for precision machining processes.