In the dynamic world of modern manufacturing, silicone molding quietly emerges as an unsung hero, silently revolutionizing the way industries across the spectrum craft products, from intricate prototypes to mass-produced components. In this comprehensive guide, we invite you to explore the remarkable world of silicone molding and how it can breathe life into various sectors.
Understanding Silicone Molding
Silicone molding, sometimes referred to as silicone rubber molding, represents an innovative, flexible, and highly efficient manufacturing method. At its core, it leverages the unique properties of silicone rubber to create molds for an impressive array of parts and products. Its extensive utility is driven by a host of compelling advantages, including:
- The ability to craft complex shapes and intricate designs.
- The capacity to produce parts with exceptional detail.
- The creation of parts with a smooth surface finish.
- Resistance to the harshest conditions—heat, cold, and chemicals.
- The development of reusable parts.
Silicone molding stands as an extraordinarily versatile and cost-effective manufacturing technique that serves a broad spectrum of purposes.
The Versatility of Silicone Molding
Silicone molding transcends industry boundaries, adapting to the unique requirements of different sectors. Let’s take a closer look at how this versatile method finds its place in various industries:
1. Automotive Industry
In the fast-paced world of automotive manufacturing, precision and durability are non-negotiable. Silicone molding plays a pivotal role in crafting intricate automotive components, from gaskets and seals to engine parts. It ensures a perfect fit, reducing noise and vibration. The durability of silicone makes it an ideal choice for automotive applications, as it can withstand extreme temperatures and pressures while resisting wear and tear.
Notable automotive parts made using silicone molding include:
- Engine gaskets
- Door seals
- Window seals
- Windshield wiper blades
- Air filter housings
- Fuel tank caps
- Oil filler caps
- Radiator hoses
- Brake hoses
2. Medical Device Manufacturing
Silicone molding takes center stage in the medical field, enabling the creation of prosthetics, orthopedic devices, and various medical components. The biocompatibility of silicone rubber ensures it’s safe for use in the human body. Additionally, its strength and durability make it a reliable choice for medical applications. Silicone molding offers precision that’s crucial for designing complex medical devices that enhance people’s quality of life.
3. Electronics and Consumer Goods
When it comes to producing consumer electronics and gadgets, silicone molding offers a cost-effective solution. It facilitates the creation of custom silicone keypads, seals, and casings, enhancing the overall user experience. Silicone’s durability, flexibility, resistance to environmental factors, and non-toxic nature make it a safe choice for products in contact with the skin. Furthermore, the quick and straightforward silicone molding process reduces production costs.
4. Aerospace Industry
In the aerospace sector, precision and reliability are paramount. Silicone molding is the go-to choice for crafting components for aircraft, ensuring they can withstand extreme conditions while performing flawlessly. Silicone’s versatility, resistance to harsh conditions, and precision in molding make it indispensable in manufacturing components for aircraft, where safety and quality are of utmost importance.
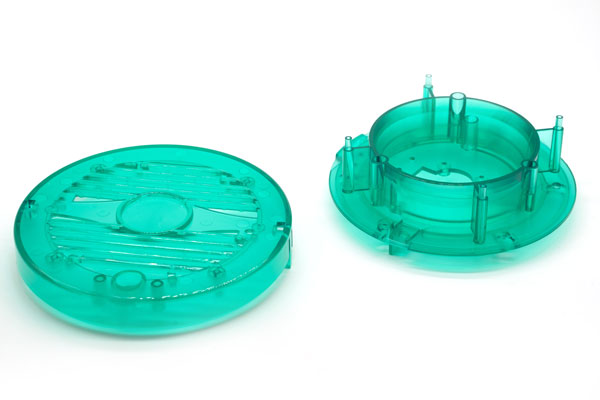
rapid-prototyping-services
5. Prototyping
Silicone molding shines as a valuable tool for rapid prototyping. Designers and engineers can swiftly create prototypes to test their innovations, reducing time-to-market for new products. Silicone molds are cost-effective to produce and can withstand repeated use, making them ideal for multiple iterations during the design and development process.
The Silicone Molding Process
Step 1. Mold Design and Creation
The journey begins with meticulous mold design tailored to the product’s exact specifications. This flexibility ensures that even the most complex shapes and sizes can be replicated with ease.
Step 2. Material Selection
Silicone rubber selection is a crucial step, with considerations including hardness, color, and specific properties required for the final product.
Step 3. Molding
The silicone rubber is carefully mixed and poured into the mold, followed by curing to produce a durable and flexible silicone component.
Step 4. Demolding
After curing, the mold is carefully removed, unveiling the finished product. The demolding process is delicate, ensuring the product retains its shape and intricate details.
Benefits of Silicone Molding
- Precision: Silicone molding delivers parts with incredibly tight tolerances, a boon for applications where precision is paramount, such as medical devices and aerospace components.
- Cost-Effectiveness: Compared to other methods requiring expensive tooling, like injection molding, silicone molding proves to be a cost-effective solution, especially for low to medium-volume production.
- Durability: Silicone’s exceptional durability allows it to thrive in diverse conditions, including extreme temperatures, exposure to chemicals, and heavy wear and tear.
- Customization: Silicone molds can be easily tailored to produce unique parts and products, ideal for applications where variety and customization are key.
Conclusion
Silicone molding stands as an indispensable asset in the manufacturing industry. Its exceptional versatility, precision, and cost-effectiveness make it a top choice for various sectors, including automotive, medical, electronics, aerospace, and prototyping.
These molds are capable of creating a wide range of products, from small, intricate components to large, complex assemblies, all with minimal wear and tear. Their cost-effectiveness and ease of maintenance further reinforce their position as a favored manufacturing solution.
In conclusion, silicone molding emerges as a versatile, precise, and cost-effective manufacturing process, well-suited for a wide range of applications.
Ready to explore the endless possibilities of silicone molding for your manufacturing needs? Contact RISE, your trusted partner in manufacturing innovation, and unlock a world of possibilities. Your journey to superior quality and cost-effective solutions begins here.