Vacuum Casting
A complete turnkey solution based on your designs
Parts as fast as 3 Days
From 1 to 50+ parts
What is Vacuum Casting?
Vacuum casting would be a quick and low-cost prototyping technology, which is referred as polyurethane casting or urethane casting. It is a process that puts some liquid materials like plastics or rubber to a silicone and then uses a vacuum to create complex components. It used to make small batches (up around 20) of exact polyurethane construction components. Seemingly, it is a good method that replaces injection molding because it is comparatively lower than others.
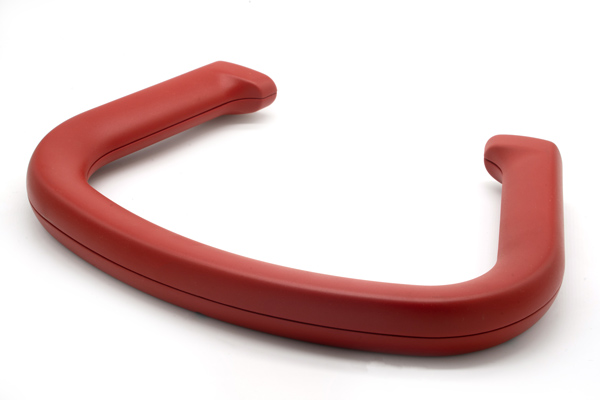
How Many Steps in the Process
Vacuum casting and injection molding are largely identical but with minor differences. The differences between them is in the types of molds used and where injection mold tools are made from metal, vacuum casting always uses silicone molds.
- The first step in the process is to create a 3D CAD model for the project. It can be regarded as the guideline used for making the silicone molds in the following steps. It is made from some materials with high durability such as metals and plastics.
- According to the 3D file, we create the master mold by 3D printing techniques like SLS or SLA. It is much faster.
- After making the master mold, we prepare to make silicone molds. Silicone molds are made by the master mold and a casting box. Pour the molten silicone into the box, which is around the master pattern. Waiting about 8-16 hours, the silicone has solidified. We operate the whole process under the condition of vacuum.
- Then, mix and pour the polyurethane resin into the bowl of the machine.
- Last, demold the casted parts.
Why Do You Need the Process
The condition of vacuum makes sure that there are no bubbles in the mold, and it removes any resistance. The first factor we consider in selecting vacuum casting is quality. It takes for granted that we can have the high quality and same parts. Besides, it is a highly economical and efficient manufacturing way for making complex and intricate workpieces.
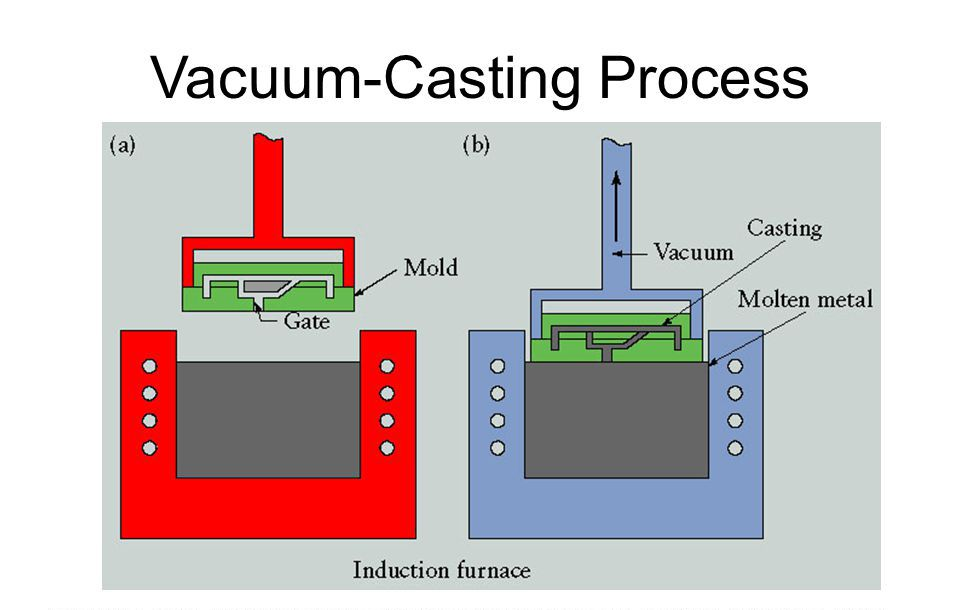
Advantages of the Process
- The items manufactured using this technology are of exceptional grade. It can be said that the demold parts will be the same as the masterpiece, so that we would not worry about the excellent quality.
- It can be used to create small batches of parts. And it runs with little volume.
- Accuracy and fine detail. Complex and intricate shapes can be easily manufactured with high precision.
How Does Defect Occur in Vacuum Casting?
- Gas porosity
This is the formation of bubbles within the process after it has cooled. While the part solidifies in a mold, it would release the gas. There will be a condition that the gas bubbles get trapped inside it. So that it would become the faulty product.
- Shrinkage porosity
This type of defect always happens in either the cope or drag portion of the casting. It forms the top of the hot pots and then the impurities and gas would cause the defects occurred.
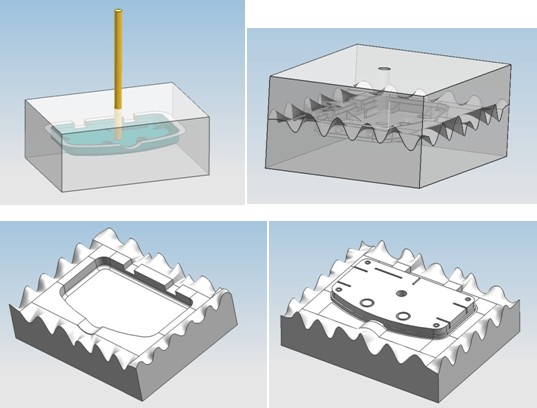
The Efficiency of this Process
With vacuum casting, that is feasible to accomplish a rapid turnaround for parts. This SLA tool gets completed in 4 weeks. Each day, about one-two pairs, are cast. Tool wear is typically between 20 & 25 pieces due to the materials and sophistication of the component, though it might be as cheap as five and as expensive as 100. Last but not least, vacuum casting would be a cost-effective method of producing elevated prototypes or targeting pre-series items.
Uses of Vacuum Casting
This technique is applied in the commercial products industry extensively. There are some applications of it as followed.
- Consumer products manufacturing
Consumer products made more efficiently using vacuum casting.
- Electronic industries
Vacuum casted parts have excellent heat resistance. It is a preferred method for making housing s of electronic devices.
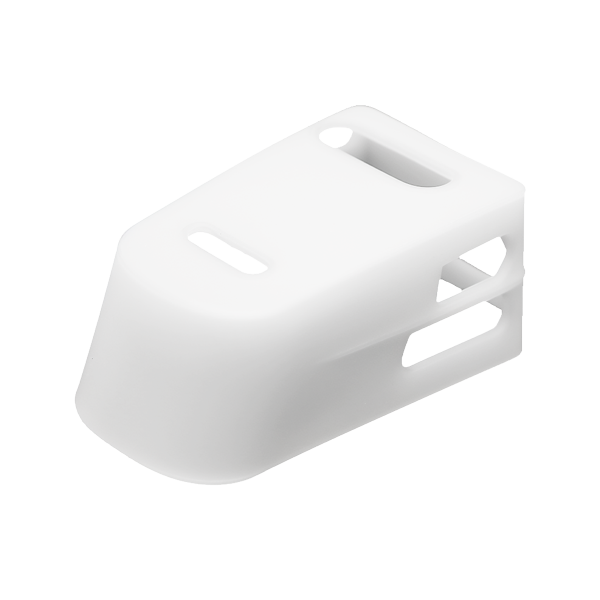
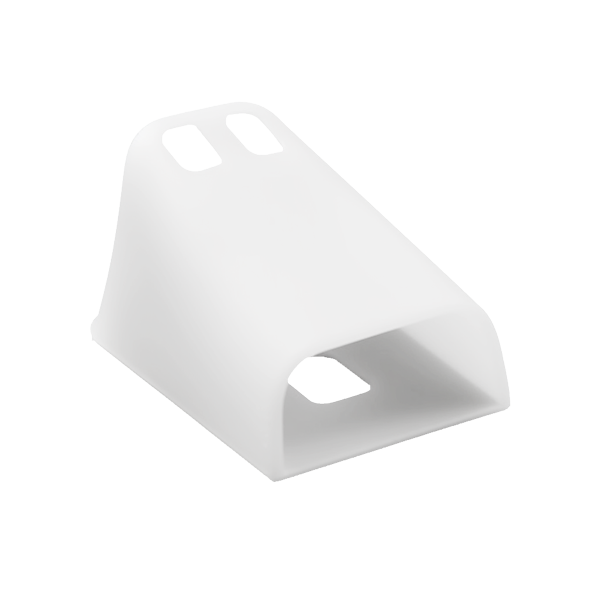
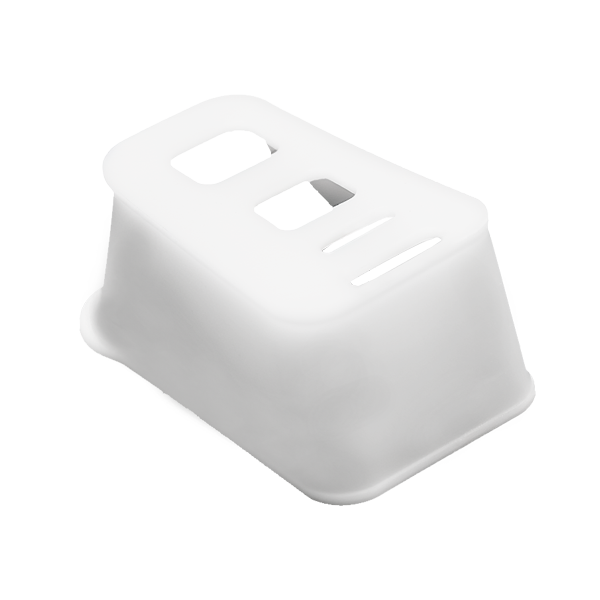
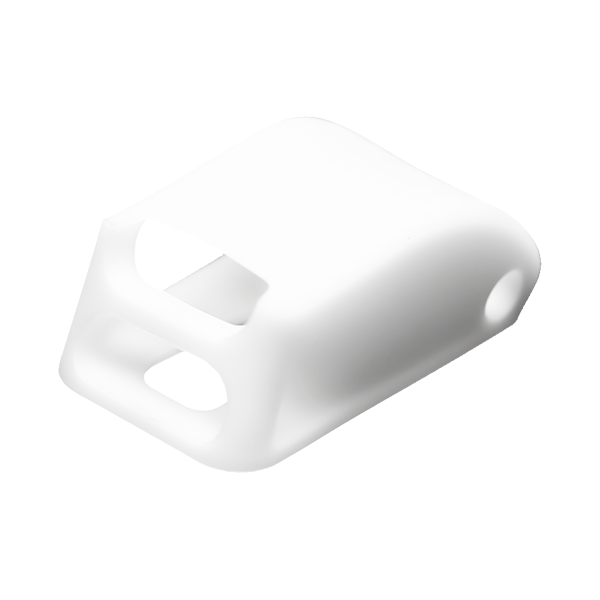
Ready to start your next project?
Contact us and get a quote in 24 hours