Rapid Tooling
P20 Tool Steel
Free DFM Support
Finished Mold as Fast as 7 Days
What is Rapid Tooling?
Rapid tooling got started in 1990s. It is the process that creates a prototype in a short time. Nowadays, before the high volume and full scape production, rapid tooling is ideal for prototyping a model and make a few hundred parts. It becomes an excellent solution to test and evaluate the part whether we want or not. Prefabrication may complete using various approaches. Microfabrication methods include electronic CAD/CAM samples, manufactured production parts, 3d printing technology prototypes, and CNC manufactured models.
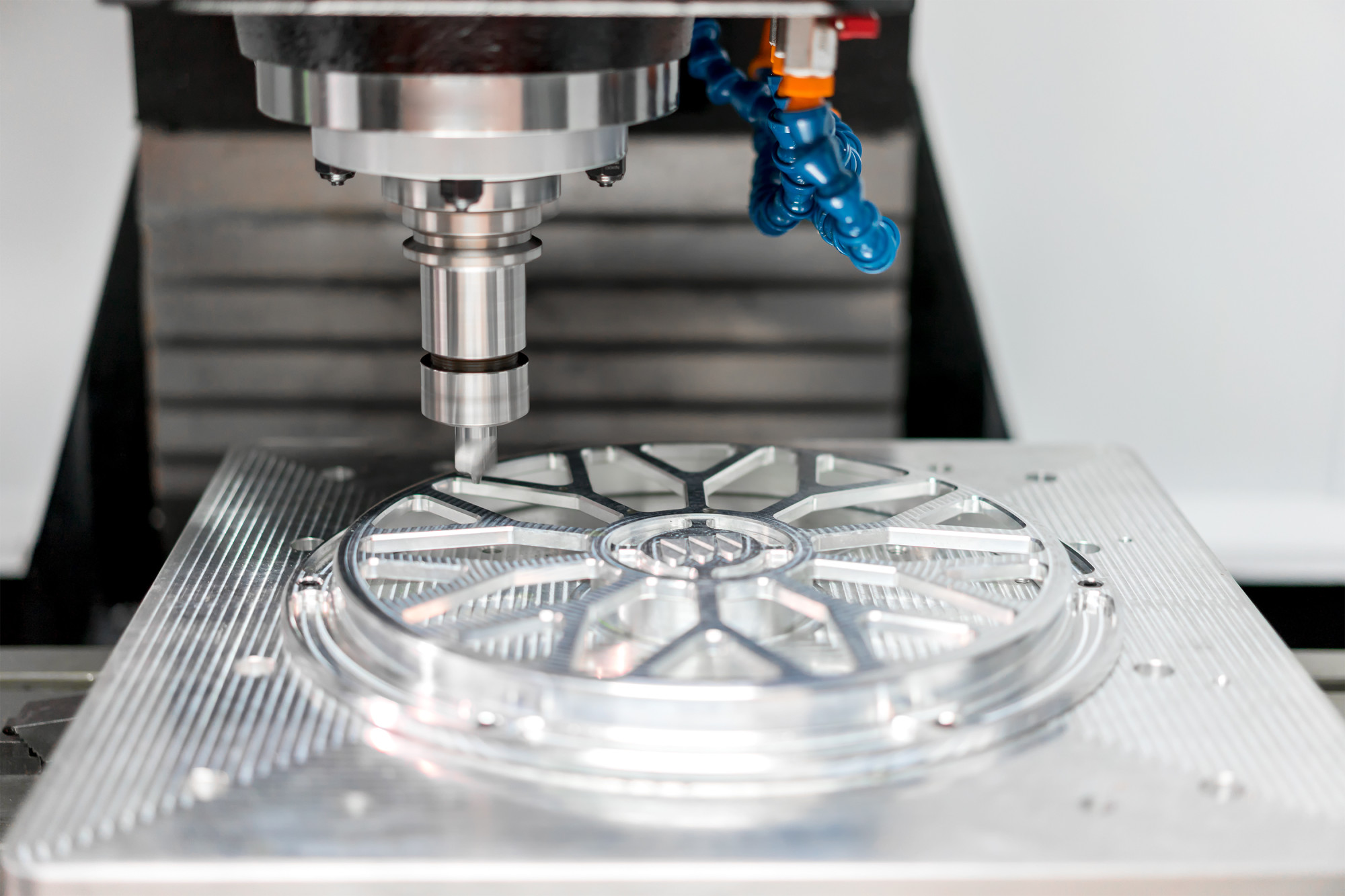
Advantages of Rapid Tooling
For entrepreneurs, it may be hard to choose the right method in production. The cost would be an essential consideration. Each manufacturing method would have its own set of processes and strengths, so does rapid tooling. Evaluate your budgetary allocations before deciding on a method to reduce overpaying. Prototype production is required to save future costs.
With this technique, we can get benefits from it as followed.
- Time and Cost Saving
Fast production speed is one of the critical advantages of rapid tooling. Traditional process takes few months to deliver to the market while rapid tooling only needs weeks or even days. Besides, this manufacturing method helps entrepreneur’s production with tighter budgets.
- More opportunities for innovation and optimization
Because of its fast production feed and low costs, it initiates up a new range of opportunities for improvements.
- Many kinds of materials can be used
It allows to create parts with any materials with different dimensions. This helps clients find the most suitable type as the material.
How Many Steps in the Process
There are few steps are involved in the rapid tooling process.
- Designing ideations
This is the first step of beginning the project. We should consider the measurement and placement of features, assembly process design, certification and others during this stage. After finishing the concept, we could make it reality.
- 3D file generation
We could set up the 3D file according to our idea. In the 3D file, the sizes of workpiece, functionalities and visualization can be completed and showed to us.
- Identification of the production sequence
In addition, the sequence of production processes is determined to construct the prototype using a continuous precision machining operation. And then, we create a tool and mold model using Computer-Aided Design (CAD) software.
- Production
If the prototype can be passed by clients, we can create the actual mold. It is available for making parts. And we can bring it on stream.
Why Do You Need the Process
Rapid tooling is a superior choice for clients who wants to test and evaluate the parts before the full-scale production. Due to its flexibility, lower production costs and faster delivery time to market, it becomes more significant. In particularly, rapid tooling helps any business that demands a final product with accuracy and consistency. It decreases the errors of production.
Conditions for the Process
- The mold must be strong enough to handle the injection molding process. If it is durable so that it can be survive. Besides, it has to be able to withstand the injections of hot plastic materials.
- What’s more, it not only need to be strong but to be smooth. So that it can eject cleanly for the plastic parts.
Types of Rapid Tooling
There are two main types of rapid tooling. One is direct rapid tooling, the other is indirect rapid tooling.
Direct rapid tooling takes guarantee that we will have a faster production time and delivery to the market. And its procedure has less steps to make parts. Moreover, it is very flexible in producing.
Indirect rapid tooling needs only one master pattern, which is very durable. Relatively speaking, it is more economical. And it can make tools with the complex designs and geometries.
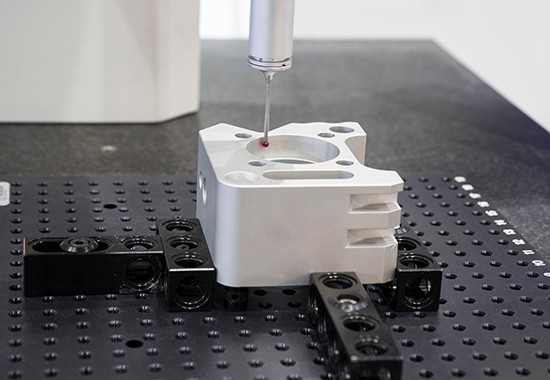
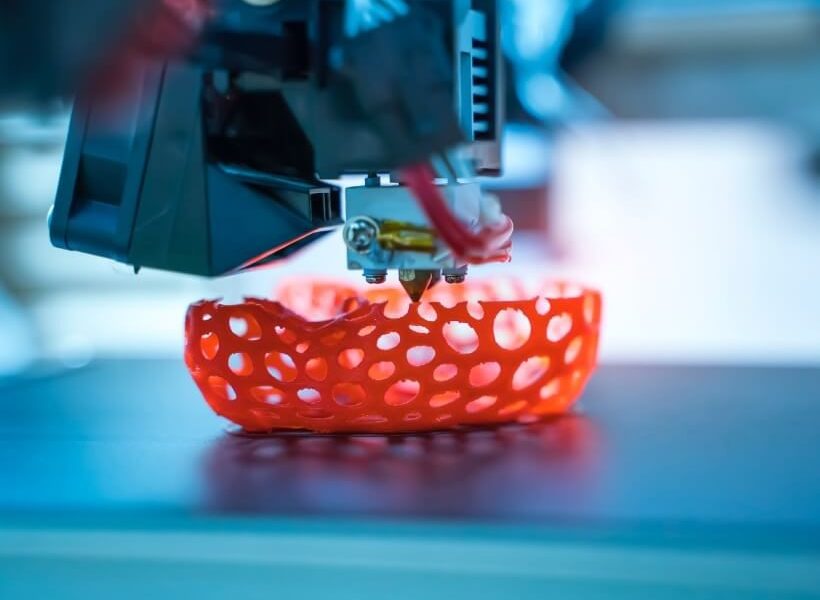
How to Get Better Results From Rapid Tooling
- Reducing surface roughness is critical in material injection molding since it can cause issues during component ejection and extend battery time.
- Article techniques like protective coatings are also enabling new quick tooling methods.
- It utilizes usual mold bases but produces inserts.
- It utilizes aluminum and mild steel, that machine more quickly.
- It helps in removing unnecessary processes, including EDM.
- This process utilizes low-cost materials and inserts made by hand.
4 Steps to Work With Us
Upload 3D Files
Upload your designs files & tell us important details about your project.
DFM Review
Comprehensive design for manufacturing analysis to optimize your parts.
Manufacturing Starts
Once you accept our quote, begin working with our team to make your ideas a reality.
Deliver Your Parts
Your custom parts are delivered straight to your doorstep.
Ready to start your next project?
Contact us and get a quote in 24 hours