Plastic Injection Moulding
Instant Quotes & DFM Feedback
Free DFM Feedback With Your Quote
Parts as Fast as 2 Days
What is Injection Molding?
This molding process is perhaps the numerous widely manipulated production technology to produce plastic items. It allows the parts to be produced in large volumes. It is ideal for almost any industries because we can see the products or components that are made of it around our life. In this way, we can create parts that are identical and dimensionally consistent, even with complex designs.
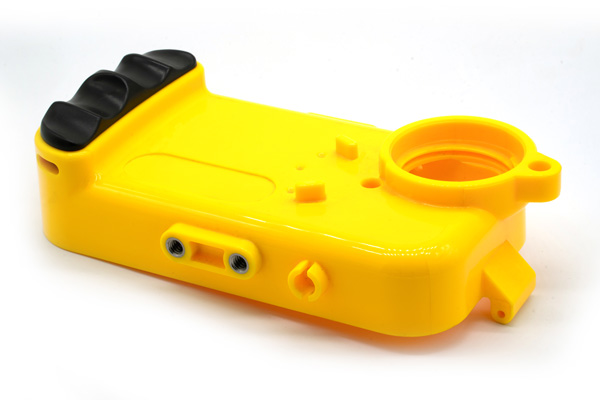
Process of Injection Molding and Its Cycles
Injection molding works with a polymer. It involves a high-pressure injection of molten plastic materials into the mold. Then, cools and solidifies to its final way. The injection molding process cycle is relatively brief, often lasting between several minutes even seconds. It comprises four stages:
Clamping
Before the mold is injected with molten materials, the gripping device must firmly close the two decay areas. Next, the materials are injected as the clamping unit pushes the halves together.
Injection
The plastics are injected into the machine, which uses the heat to melt the materials. Injection time can be estimated by other factors such as injection pressure, power and short volume. The injection pressure can range from 35-140 MPa.
Cooling
The mold begins to cool after it approaches to the interior mold. Only when the cooling period has elapsed can the mold be opened. After it cools down, we can get the shape what we want.
Ejection
The last step is ejection from the operation machine. It is employed to push the entity out of the decay. We need to push the part out with forces because it would shrink and stick on the mold.
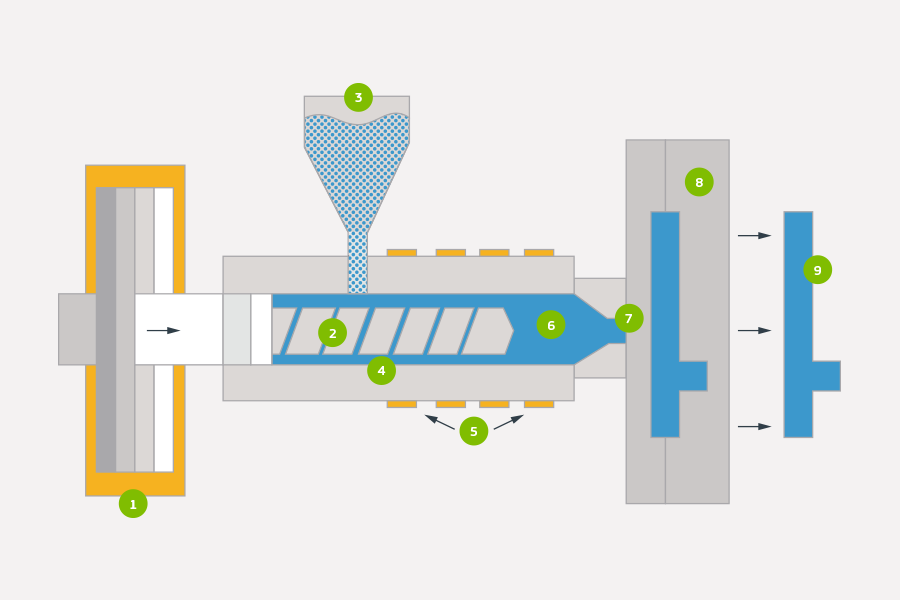
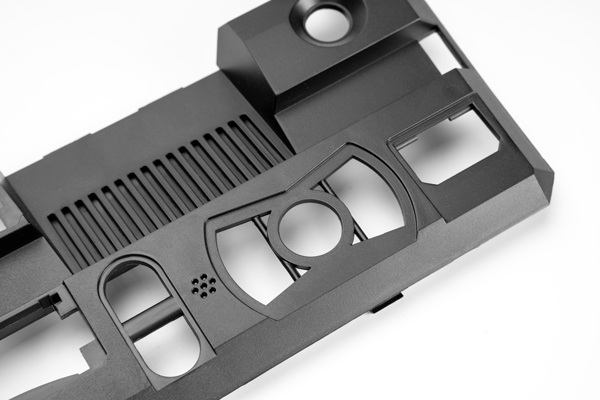
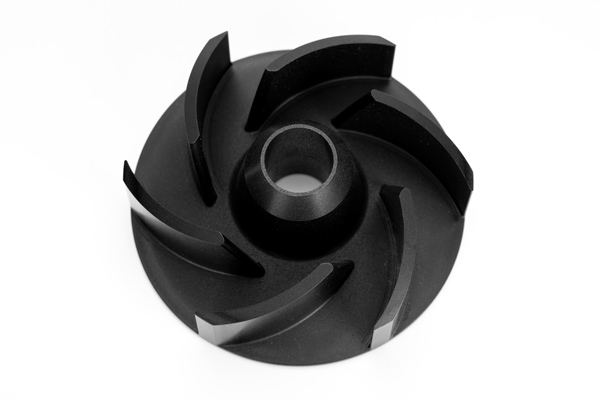
Advantages of Injection Molding
- High productivity
The actual molding process is much more rapid than another molding customer’s specifications, and the press has been well earlier. It has a fast production rate and is able to make mass plastic parts in a single cycle.
- Increased strength and highly repeatable
Filter used in injection molds in the injection molding process. These scopes assist in raising the immobility of the item behind its decay by lowering the textile’s densities while it is starting. It can produce many parts with same forms and dimensions. It is guaranteed to be identical.
- Make complex parts
Through the injection molding, the parts can be intricate. Overall production time can be shaved down.
- Make use of repetition and consistency
Injection molding is a relatively reproducible process. That seems to be whatever the second section you create will be essentially equal to that, and so on. It is a fantastic trait to have when trying to achieve brand consistency & part dependability in big volume production.
How to Optimize the Tolerances
- We can prevent the tolerances in the step of design. We can anticipate the potential warping and control it in minimum.
- Select the most suitable material for the project. Because the tolerances of plastic parts would be impacted by different materials.
- Well-designed tools play an integral role in ensuring that parts cool properly and adhere to strict injection molding tolerance standards.
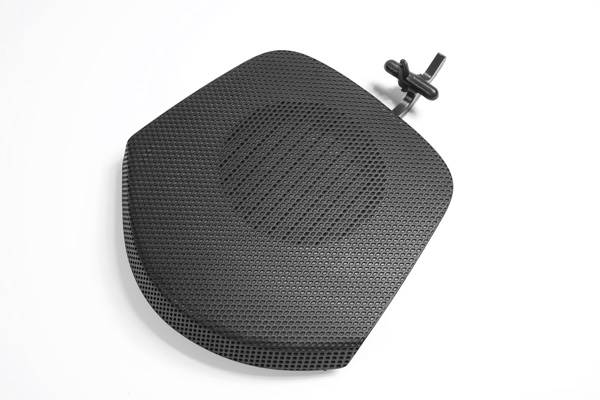
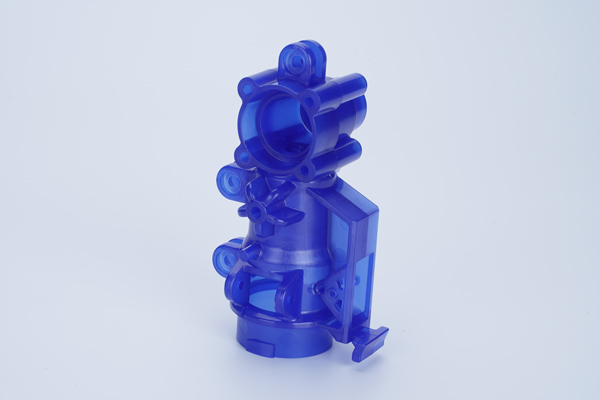
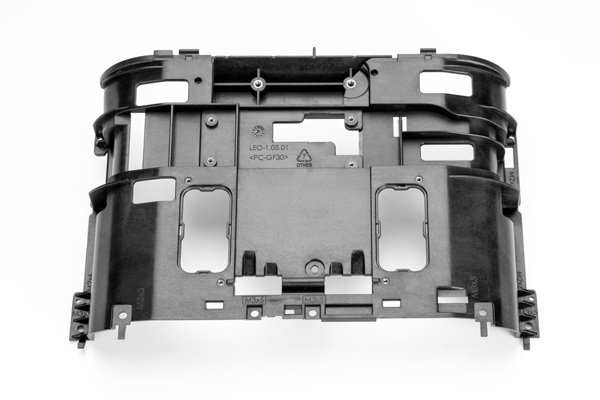
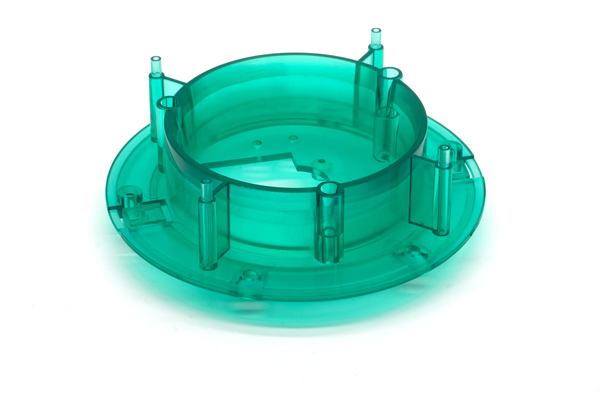
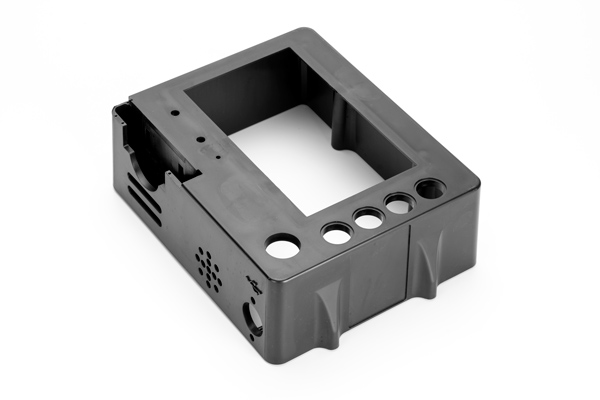
Ready to start your next project?
Contact us and get a quote in 24 hours