Amidst the dynamic landscape of manufacturing, Rapid tooling emerges as a crucial intermediary between the realms of innovation and production. Through its pioneering approach, Rapid tooling has revolutionized the transition of prototypes into full-scale manufacturing operations, optimizing processes and amplifying efficiency.
The Essence of Rapid Tooling
Amidst the dynamic landscape of manufacturing, where swiftness and productivity reign supreme, Rapid tooling emerges as a groundbreaking paradigm. This pioneering approach dramatically expedites the transition from initial prototype ideation to full-scale mass production, empowering manufacturers to iterate and refine their designs with remarkable velocity and unparalleled accuracy.
The Power of Rapid Tooling
Rapid tooling involves the swift and efficient creation of tooling molds, which are essential for shaping and producing parts. Traditional methods of mold-making can be time-consuming and costly, often hindering the pace of product development. However, Rapid tooling streamlines this process by utilizing advanced technologies such as 3D printing, CNC machining, and injection molding. These technologies enable the rapid fabrication of complex and precise molds, significantly reducing lead times and production costs.
Seamless Transition from Prototype to Production
Rapid tooling seamlessly bridges the gap between prototyping and mass production. In the past, manufacturers had to endure lengthy and iterative cycles of prototyping, testing, and mold-making before reaching the production stage. This often resulted in delays, increased expenses, and potential design compromises. With Rapid tooling, manufacturers can swiftly validate their prototypes, incorporate feedback, and move directly into production. This streamlined process eliminates bottlenecks, minimizes risks, and allows for faster time-to-market.
Benefits of Rapid Tooling
The advantages of Rapid tooling extend far beyond speed and efficiency. Here are some key benefits that make it a compelling choice for manufacturers:
- Cost Savings: Rapid tooling significantly reduces the costs associated with traditional mold-making. The use of advanced technologies minimizes material waste, eliminates the need for expensive tooling equipment, and reduces labor hours.
- Design Flexibility: Rapid tooling allows manufacturers to experiment with different design iterations quickly and easily. This flexibility enables them to explore innovative concepts, optimize product performance, and respond to market demands with agility.
- Improved Quality: Rapid tooling ensures higher precision and accuracy in the production of parts. The use of cutting-edge technologies minimizes human error and maintains consistent quality throughout the manufacturing process.
- Reduced Lead Times: With Rapid tooling, manufacturers can significantly reduce the time required to bring products to market. This accelerated timeline provides a competitive edge, enabling businesses to capitalize on market opportunities and respond to customer needs promptly.
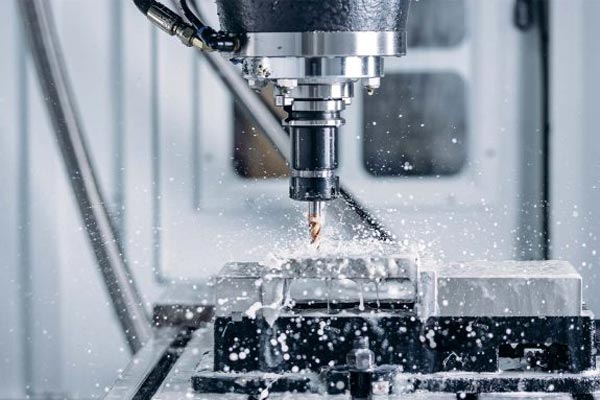
CNC machining prototypes
Unleashing Innovation with Precision Molds
Precision at Every Stage
The heart of Rapid tooling lies in the creation of precise molds. These molds ensure that each component of the final product maintains the desired specifications. The meticulous attention to detail in mold creation guarantees a flawless end product.
Iterative Refinement
One of the standout features of Rapid tooling is its ability to facilitate iterative design improvements. Manufacturers can swiftly implement changes based on prototype testing, ensuring that the final product meets or exceeds expectations.
Bridging the Gap: From Concept to Market
Accelerated Time-to-Market
In the competitive landscape of modern business, speed is often the differentiator. Rapid tooling significantly reduces the time it takes for a product to move from the conceptualization phase to market availability, giving businesses a critical edge.
Cost-Efficiency Unleashed
Traditionally, transitioning from prototype to production involved prolonged timelines and exorbitant costs. Rapid tooling disrupts this norm by minimizing both time and financial investments, making it a cost-effective solution for businesses of all sizes.
Embracing the Future of Manufacturing
In conclusion, Rapid tooling stands as an indispensable force in the manufacturing landscape, propelling innovation forward. Its ability to seamlessly connect prototype development with mass production not only saves time and resources but also opens doors to unprecedented levels of creativity and efficiency. As businesses navigate the path from concept to market, Rapid tooling emerges as the key enabler, unlocking a future where ideas materialize at the speed of innovation.