Understanding rapid prototyping techniques means you aren’t limited to one choice when selecting the right methodology for your prototyping project. It’s also important to note that rapid prototyping doesn’t require limitations to a single process to get results.
There are several rapid prototyping technologies available for product design engineers.
Additive manufacturing
- Stereolithography (SLA)
- Selective laser sintering (SLS)
- Direct metal laser sintering (DMLS)
- Fused Deposition Modelling (FDM)
- MJF
- Binder jetting
- Poly jetting
Other Rapid prototyping techniques include the following.
- CNC Machining
- Vacuum casting
- Investment casting
Understanding the differences between these methods and the advantages of each is beneficial to effective, rapid tooling assembly and the fast track to mass production.
Vacuum Urethane Casting
Urethane or vacuum casting utilizes silicone molds to manufacture rubber and plastic components in a vacuum. It’s one of the top-rated rapid prototyping processes available for injection molding plastic parts.
So, it’s ideal for pre-production prototype parts requiring small to medium volumes for functional and stress testing purposes.
Vacuum casting Advantages
- A broad range of resins is available for vacuum casting parts.
- Produce small part patches with high quality and accuracy.
CNC Machining
This process is the best choice for components relying on tolerance and accuracy. CNC machining describes a “subtractive” process where tooling moves along up to four axes, removing material from a workpiece. Workpiece materials include various options in metals and plastics to cater to a broad range of applications.
In rapid prototyping projects, CNC machining is the best choice for components with critical features to save on costs as it’s an expensive prototyping method.
CNC Machining Advantages
- Great surface finish and high-level accuracy.
- Plenty of material options in metals and plastics.
Direct Metal Laser Sintering (DMLS)
This additive manufacturing technology involves the melting and fusing of metallic dust using a high-power laser operated by computer algorithms. Most alloys are compatible with DMLS, allowing for the production of full-strength, functioning prototypes with hardware produced in a similar material to the mass-production components.
DMLS Advantages
- It’s compatible with materials like aluminum, titanium, stainless steel, and other alloys.
- Excellent strength properties.
- Ideal for producing features and shapes challenging for CNC machining methods.
Stereolithography (SLA)
The Stereolithography method (SLA) utilizes a laser to cure the resin with UV rays, creating parts from a selection of liquid resins. They’re ideal for low-end but functional prototypes, molds, patterns, and production tooling.
SLA offers product engineers and designers the ability to create prototypes fast, providing an excellent surface finish and high dimensional accuracy. SLA works with all durable, tough, elastic, flexible, and rigid resins.
Stereolithography (SLA) Advantages
- Reasonably priced
- Excellent surface finish for AM parts
- Mature technology with a comprehensive material selection
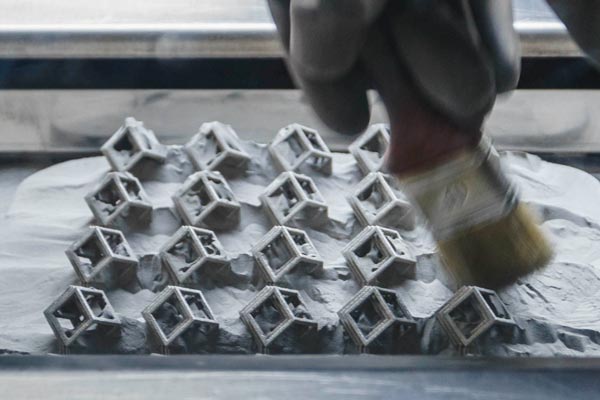
3d printing products
Selective Laser Sintering (SLS)
SLS also utilizes a laser in component manufacturing. It forms functional parts using a sintering process on polymer powders. The internals of SLS parts are usually porous. That means they have excellent tensile strength despite being brittle.
Typically, SLS processes offer larger volumes, generating components with complex geometry. It’s also a good rapid prototyping choice for long-lasting parts. You get low cost per unit, high production rates, and a range of materials to suit applications ranging from small-batch manufacturing to quick prototyping.
SLS prototypes are available in materials like PA11, PA12 Carbon-filled, PA12 glass-filled, PA12 flex, P12, and TPU.
SLS Advantages
- Excellent durability with a high degree of accuracy.
- No support structure is needed.
- Suitable for coloring and dying.
Fused Deposition Modelling (FDM)
FDM tech models 3D parts by melting materials like thermoplastic resins and extruding them onto build platforms in a layering method before letting them solidify. FDM printers have benefits in the rapid prototyping process because they can print in composites and polymers, creating desirable, lasting parts. FDM printers can develop prototypes in various materials, including PC-ABS, ABS, ASA, or Nylon.
FDM Advantages
- More affordable or prototyping projects compared to SLS and SLA.
- Ideal for making complex components.
- Compatible with a range of thermoplastic resins.
Multi Jet Fusion (MJF)
Multi-jet fusion is a powder bed fusion 3D printing technology in which a fusing agent bonds powdered material and then heats to fuse them to produce 3D parts. MJF can print highly accurate and durable rigid parts using Nylon PA11, PA12 Nylon, and PP. They can also print flexible TPU parts.
MF Advantages
- One of the fastest 3D printing methods.
- Powder bed means no support structure required.
- Great surface finishes and physical and mechanical properties.
Poly Jetting
This material jetting tech produces accurate, smooth prototype components. Poly jet utilizes photopolymers to create prototype components by jetting the build platform before UV curing. This allows for a smooth surface and the introduction of colorants to component forming for concept modeling projects. Poly jetting is available for various general-purpose resins, including transparent, opaque, and rigid parts.
Poly Jetting Advantages
- Reasonable printing costs.
- Able to print thin lines and complex shapes.
- Flexible and rigid materials can combine into one component.
Binder Jetting
This is one of the seven additive manufacturing methods suitable for rapid prototyping projects. It’s capable of producing colored plastic and metal parts. In comparison to DMLS, binder jetting is affordable and a good choice for prototyping projects concerned with increased budget costs. With binder jetting, the binding agent is deposited into a powder bed to solidify and form a 3D part.
Binder Jetting Advantages
- Prototype full-scale models for testing.
- Affordable for large prototyping projects.
- Fast production process.
- Ideal for metals and plastics.
Investment Casting
This prototyping method utilizes wax patterns coated with ceramics to mold prototype components. The result is an expendable mold with the wax pattern melting away before pouring the liquid metal. After the metal cools and solidifies inside the mold, the manufacturing foundry breaks the mold and removes the casted parts.
Investment casting is ideal for die-casting prototype parts. Combining Investment casting and 3D techniques like SLA and FDM produces accurate master patterns featuring fine details and smooth surface finishes.
Investment casting is compatible with various alloys and metals, with aluminum being the preferred choice in most prototyping projects.
Investment Casting Advantages
- Cast components with complex shapes and features.
- Great dimensional accuracy.
- Tight tolerances.
- High-grade surface finish.