There are several processes available for rapid prototyping, with polyurethane casting being a top choice for manufacturers. This process utilizes silicone molds to fashion rubber and plastic components in a vacuum.
The process is similar to plastic injection molding, offering manufacturers a production facility for low-volume, high-quality plastic components. This post unpacks everything you need to know about using polyurethane vacuum casting for prototyping projects.
What are the Applications for Vacuum Casting?
- Vacuum casted components are ideal for fit, form, and functional testing during the initial embodiment and design phases.
- Vacuum casting allows for the production of one-off components for marketing purposes, field testing, and product verification.
- There are several commercially-available resins available for use in vacuum casting applications.
- These resins can satisfy a range of surface hardness, textures, and temperature requirements.
- Resins are available, producing translucent, opaque, or transparent components.
- Vacuum casting can produce wax masters for investment casting purposes, with high-quality finishes to increase the visibility of intricate features and finer details in prototypes.
Vacuum Casting for Rapid Prototyping – Unpacking the Process
Like plastic injection molding, vacuum-casted components follow specific production guidelines using a shaped cavity in a mold tool. However, while plastic injection mold tooling features design and construction with aluminum or steel, vacuum casting implements the use of a silicon mold.
Modeling 3D Parts
The first stage of the vacuum casting process is to follow design guidelines for optimal results. Designers can inspect components with a 3D laser scan to create 3D design files for production purposes.
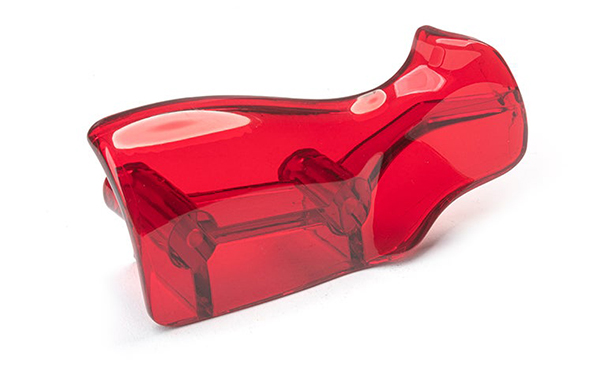
vacuum casting part
The Master Pattern
Next up is the creation of the master pattern through a CAD model. The patterns feature manufacture with materials capable of withstanding temperatures of 40°C. The components are manually finished and cleaned to finish and texture specifications. Manufacturers paint or spray the pattern to achieve a matt or gloss finish.
Manufacturing the Silicone Mold
The manufacturer then fits the master pattern with inserts, cores, and casting gates, suspending it in a casting box. Risers are added to allow for air to release from the mold. Next, the manufacturer pours silicon into the master pattern under a vacuum, where it flows into the cavity, forming the final product shape.
The manufacturer follows up by curing the pattern in an oven at 40℃ for approximately 8 to 16 hours. After curing, the risers and box are removed, and the mold split to expose the cavity. The wavy cut provides accurate, precise alignment of the halves during production.
Mix & Pour the Resin
The manufacturer preheats the polyurethane casting resin to approximately 40°C before mixing. The dual-component resin is mixed in exact quantities and proportions, and the pigment is added before being poured into the vacuum casting machine.
The manufacturer returns the mold and connects the pouring gates to the bowl. The auto-pouring of the resin ensures proper stirring and duration for approximately 50 to 60 seconds in a vacuum to avoid producing voids or air pockets.
Demold Casted Parts
After casting the resin, the manufacturer places the mold in the heating chamber for curing. After curing, the manufacturer removes the casting and the gate and risers and carries out any finishing.
In Closing – What are the Advantages of Vacuum Casting for Rapid Prototyping?
- Vacuum casting allows for the use of multiple parts from the master pattern within a 24-hour period. This action results in a reduction of the prototyping production stage, saving time and costs on development projects.
- Vacuum casting is ideal for creating small quantities of high-quality parts for the prototyping process or low-volume components for low-stress, benign environments.
- A range of vacuum-casting resins, such as rubbery, clear, flame-retardant, colored, and food-grade, are available.
- Manufacturers can switch the type of resin without retooling, allowing for the testing of different material types for prototypes.
- Manufacturers can produce complex features and shapes in components using multi-segment molds and cores.