Vacuum casting is a versatile and popular technique in the manufacturing and prototyping world. It is known for its ability to produce high-quality parts with excellent surface detail and fidelity. Vacuum casting has carved a niche for itself in various industries. But how exactly does this process work, and where is it most commonly used? Let’s dive into the intricacies of vacuum casting and explore its myriad applications.
How Vacuum Casting Works:
Master Model Creation:
The process begins with the creation of a master model. It can be fabricated using various techniques, but CNC machining and 3D printing are the most popular methods due to their precision and detail accuracy. The master model should represent the final desired product in detail, finish, and dimensions.
Casting the Part:
The resin gets poured into the silicone mold and entirely filled to avoid air bubbles; a vacuum gets applied. The vacuum ensures the resin reaches every corner of the mold, reproducing all the details of the master model. Once the resin has cured, the silicone mold gets opened to reveal the cast part.
Post-processing:
Depending on requirements, the cast part might undergo post-processing, such as painting, assembly, or other finishing touches.
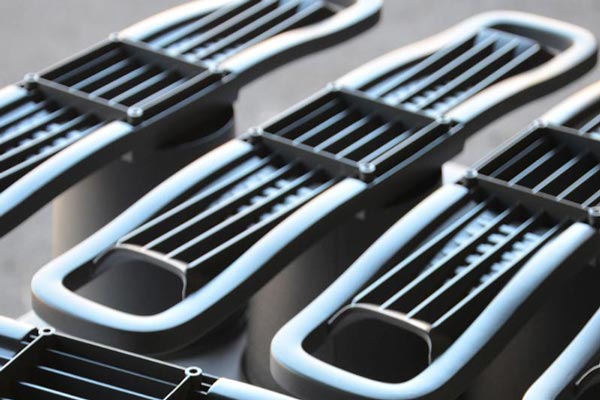
vacuum casting parts
Applications of Vacuum Casting:
Rapid Prototyping:
One of the primary uses of vacuum casting is for rapid prototyping. Due to its ability to produce parts quickly without expensive tooling, it’s a preferred method for creating prototypes to verify design, function, and fit.
Short Production Runs:
For situations where only a limited number of parts are required, vacuum casting gets best. Instead of investing in costly injection molding setups, manufacturers can produce small batches of products with vacuum casting, achieving a balance between quality and cost-effectiveness.
Medical Devices:
The accuracy and material versatility of vacuum casting makes it suitable for the medical industry, where customized devices or tools might be needed in limited quantities. Silicone molds can reproduce intricate details, ensuring medical devices meet strict specifications.
Art and Jewellery:
The sufficient detail capture of vacuum casting is particularly beneficial in the art and jewellery sectors. Artists and jewellers can create intricate designs using a master model and then replicate them with precision using vacuum casting, allowing for unique pieces or limited series.
Automotive Components:
In the automotive sector, vacuum casting finds use in producing parts for testing and design validation. Whether interior components, light casings, or dashboard elements, vacuum casting can deliver parts that closely resemble the final product in aesthetics and function.
Consumer Products:
From toys to household items, vacuum casting is employed to produce consumer products that need to be tested in the market or meant for limited edition releases.
Specialized Tooling and Fixtures:
Vacuum casting isn’t just for end-use parts. It’s also a valuable tool for creating custom jigs, fixtures, or tooling required for other manufacturing processes. While these tools might not have the lifespan of their metal counterparts, they can be produced quickly and at a fraction of the cost.
Mimicking Injection Molded Parts:
Before committing to large-scale injection molding, manufacturers can use vacuum casting to simulate the look, feel, and material properties of injection-molded parts. It can be invaluable for testing, verification, and garnering feedback.