Did you know LEGO is a Danish word that translates to “Play well?” The world’s most successful building block company is the brainchild of Ole Kirk Christiansen, a Danish carpenter. He started a company after years of building toys for his son, naming it LEGO.
In 1948, Christiansen decided to expand after years of success. Introducing injection molding in the product production process was a key ingredient of his expansion.
He invested in a plastic injection molding machine, using it to replace his traditional line of toys with plastic. The plastic mold injector offered rapid and precise replication of dozens of parts and pieces, expanding the LEGO range, and fulfilling its requirement to serve the growing demand for its products.
The first injection molds used in the LEGO manufacturing process were primitive compared to what the company uses today. Initial production runs saw the mold producing 12 blocks per run. As plastic injection molding technology advanced, LEGO kept up with the times, allowing the company to benefit from rapid prototyping and production.
Production efficiency increased, allowing for huge volumes in production runs while dropping costs and improving product quality. LEGO was responsible for many innovations in the industry, and its mold gate and runner system evolved to remove excess plastic from finished bricks automatically, providing a single-step injection molding process.
LEGO Plastic Injection Molds
The LEGO injection molds are a guarded secret held close to the company’s chest. There’s a conspiracy suggesting LEGO even buried the first molds the company created in the foundations of its new manufacturing facility to prevent its IP leaking.
Experts suggest a LEGO mold can cost $200,000 or more. The astronomical price of the tooling comes from the need for every LEGO brick to have exact, concise measurements and close tolerances.
A certified LEGO production team must frequently test the injection mold. The mold requires regular cleaning and maintenance to ensure optimal block production capacity and accuracy.
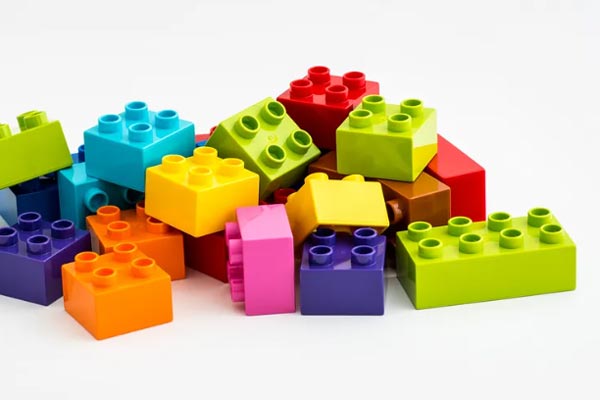
Lego bricks
How Are LEGO Blocks Made with Injection Molding?
LEGO manufactures its legendary plastic building blocks using plastic pellets heated to 450F and injected into injection molds under 25 to 150 tons of pressure. The molding process lasts approximately seven seconds before the blocks are ejected onto a conveyor belt to cool and cure.
All LEGO blocks fit perfectly with each other. This consistency has occurred across the entire LEGO product range from the 1950s to today. LEGO releases new sets every year, but every block in every set is fully interchangeable with similarly shaped blocks in other sets.
LEGO size tolerances are approximately 0.0005. That’s around half of a thousandth of an inch. Thanks to the consistency offered by plastic injection molding, LEGO blocks are timeless regardless of when purchased.
The polymer used in LEGO block production is highly durable and very strong. According to LEGO, its blocks can withstand 950 lbs of force. The compact cellular block design and military-grade polymer mean LEGOs last for decades, maintaining the ability to fit together seamlessly.
The Modern Era of LEGO Manufacturing
LEGO is still one of the biggest names in toy brands in 2023. The company sells millions of sets annually, minting nearly 75 billion LEGO bricks each year. There are over 3,700 brick varieties, and the company manufactures everything internally. Plenty of competitors have imitated the bricks, but none of them managed to compete with LEGO’s market dominance.
LEGO is introducing best practices into its production process to comply with green production quality standards. The goal of the initiative is to eliminate unnecessary plastic waste.
LEGO plans to introduce a new plant-based polymer to its brick manufacturing process. Its revamping of the conventional plastic molding process allows the company to recycle and reuse any damaged or incomplete parts rather than discard them as plastic waste.