In the realm of modern manufacturing, Computer Numerical Control (CNC) machining stands as a pinnacle of precision, efficiency, and versatility. From intricate automotive components to aerospace parts and even delicate medical devices, CNC machining plays a vital role in shaping various industries. This article delves into the fundamentals of CNC machining, its applications, advantages, and its transformative impact on the manufacturing landscape.
Understanding CNC Machining:
CNC machining involves the use of computerized controls to manipulate machine tools and execute precise machining operations on various materials such as metals, plastics, wood, and composites. Unlike conventional machining techniques that rely on manual intervention, CNC machining automates the process, allowing for higher accuracy, repeatability, and faster production cycles.
Key Components and Processes:
A typical CNC machining setup comprises several key components, including the CNC controller, machine tool, cutting tools, and work piece. The CNC controller interprets digital instructions, typically in the form of G-code, and translates them into specific movements and operations. The machine tool, equipped with motors and actuators, executes these instructions with exceptional accuracy.
The machining process itself involves a series of operations such as milling, turning, drilling, and grinding, each tailored to achieve precise geometries and surface finishes. CNC machines can operate in multiple axes (commonly three to five axes), enabling complex part geometries to be manufactured with ease.
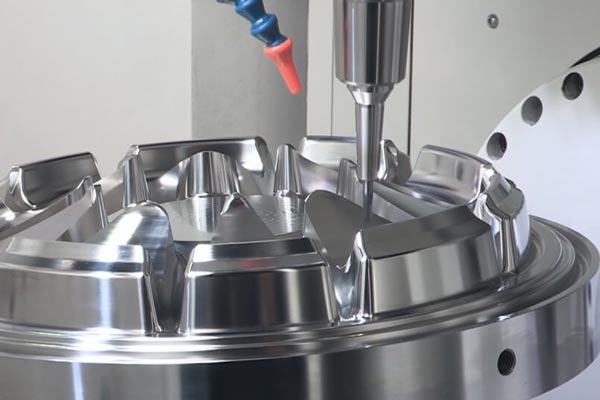
CNC aluminum part
Applications Across Industries:
The versatility of CNC machining makes it indispensable across a wide range of industries. In automotive manufacturing, CNC machines fabricate engine components, transmission parts, and chassis components with tight tolerances, ensuring optimal performance and safety. In aerospace, CNC machining produces lightweight yet robust aircraft components, contributing to fuel efficiency and structural integrity.
The medical sector benefits from CNC machining for the fabrication of prosthetics, surgical instruments, and implantable devices, where precision and biocompatibility are paramount. Additionally, industries such as electronics, energy, and consumer goods rely on CNC machining for prototyping, customization, and mass production of intricate parts.
Advantages of CNC Machining:
The implementation of CNC machining provides some prominent benefits over modern machining methods:
Precision: CNC machines can achieve exceptionally tight tolerances, resulting in parts with consistent dimensions and high accuracy.
Efficiency: Automation reduces human error and enables uninterrupted operation, leading to faster production cycles and reduced lead times.
Flexibility: CNC machines can swiftly switch between different tooling and part configurations, facilitating rapid prototyping and production changes.
Complexity: With multi-axis capabilities, CNC machining can produce complex geometries and intricate designs that would be challenging or impossible with manual methods.
Cost-effectiveness: While initial setup costs may be higher, CNC machining ultimately reduces labor costs, material wastage, and the need for secondary operations, leading to long-term savings.
Challenges and Future Trends:
Despite its numerous advantages, CNC machining isn’t without challenges. Maintaining and programming CNC machines require skilled personnel, and initial investments can be substantial. Moreover, optimizing machining parameters and tooling selection demands expertise to maximize efficiency and quality.
Looking ahead, advancements in CNC technology continue to drive innovation in manufacturing. Integration with Artificial Intelligence (AI) and machine learning enables predictive maintenance, real-time optimization, and adaptive machining strategies, further enhancing productivity and quality. Additionally, the advent of additive manufacturing technologies complements CNC machining, offering new avenues for hybrid manufacturing processes and intricate part geometries.
CNC machining stands as a cornerstone of modern manufacturing, combining precision, efficiency, and versatility to meet the demands of diverse industries. From automotive and aerospace to healthcare and beyond, CNC machining continues to redefine the boundaries of what’s possible, driving innovation and propelling industries forward in the digital age. As technology advances and capabilities expand, the future of CNC machining promises even greater efficiency, customization, and sophistication, shaping the landscape of manufacturing for years to come.