In the dynamic landscape of product development and manufacturing, the ability to quickly iterate designs and produce low volumes of high-quality parts is essential. Vacuum casting, also known as silicone molding or urethane casting, has emerged as a cost-effective and efficient solution for prototyping and small-batch production. This article delves into the intricacies of vacuum casting, its applications, advantages, and why it’s a go-to method for turning concepts into reality.
Understanding Vacuum Casting:
Vacuum casting is a versatile manufacturing process that involves the replication of master patterns using silicone molds and polyurethane resins. It enables the production of complex geometries and intricate details with remarkable accuracy and surface finish. The process begins with the creation of a master pattern, typically fabricated using 3D printing or CNC machining, which serves as the template for the silicone mold.
The vacuum casting process comprises several key steps:
Master Pattern Creation: The initial step involves designing and fabricating the master pattern using CAD (Computer-Aided Design) software and additive or subtractive manufacturing techniques.
Mold Making: A silicone mold is created by pouring liquid silicone around the master pattern and allowing it to cure. The mold is then cut open to remove the master pattern, leaving behind a negative cavity that perfectly replicates the desired geometry.
Resin Casting: Once the mold is prepared, polyurethane resin is injected into the cavity under vacuum pressure. The vacuum helps remove air bubbles and ensures complete resin infiltration, resulting in void-free parts with consistent material properties.
Curing and Demolding: The resin is allowed to cure within the mold, typically under controlled temperature and humidity conditions. Once cured, the mold is opened, and the newly cast parts are carefully removed, ready for finishing and post-processing.
Applications Across Industries:
Vacuum casting finds widespread use across a diverse range of industries, including automotive, aerospace, consumer electronics, healthcare, and more. In product development and prototyping, vacuum casting enables designers and engineers to quickly produce functional prototypes for testing, validation, and market evaluation.
In the automotive sector, vacuum casting is utilized for the rapid fabrication of interior components, trim panels, and functional prototypes of mechanical parts. Similarly, in aerospace engineering, vacuum casting facilitates the production of lightweight, high-strength components with intricate features, ideal for testing and validation before full-scale production.
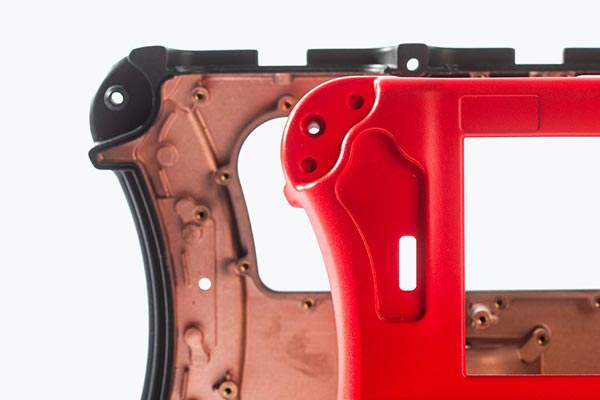
Vacuum casting products
The adoption of vacuum casting offers several notable advantages:
Speed: Vacuum casting enables rapid iteration and short lead times, allowing designers to quickly refine concepts and bring products to market faster.
Cost-effectiveness: Compared to traditional machining or injection molding, vacuum casting offers significant cost savings, particularly for low-volume production runs.
Versatility: Vacuum casting can accommodate a wide range of part geometries, including undercuts, thin walls, and complex features, without the need for costly tooling modifications.
Material Options: A variety of polyurethane resins are available, offering different mechanical properties, colors, and finishes to suit specific application requirements.
Quality and Surface Finish: Vacuum casting produces parts with exceptional surface finish and detail resolution, making them suitable for visual prototypes, marketing samples, and end-use components.
Vacuum casting stands as a versatile and cost-effective solution for prototyping and low-volume production, offering speed, flexibility, and high-quality parts with intricate details. From concept validation to end-use components, vacuum casting continues to empower designers, engineers, and manufacturers to innovate and iterate with confidence. As technology evolves and processes mature, vacuum casting remains a vital tool in the modern manufacturing toolkit, bridging the gap between imagination and realization in the ever-changing landscape of product development.