The field of rapid prototyping continues to progress, and new technology enters the industry. Innovations in machinery, materials, and processes show great promise for rapid prototyping projects in the future. Here are ten of the top trends we see for rapid prototyping in 2024.
1 Advancements in Additive Manufacturing Processes
Additive manufacturing, also known as 3D printing, is one of the rising stars in high and low-volume manufacturing. 3D printing solves the challenges presented by conventional manufacturing processes, such as die-casting.
It’s perfect for repaid prototyping processes and ideal for high-volume production of thousands of units per production cycle. 3D printing allows for the mass production of multi-material, multi-colored components.
Manufacturers get the advantage of a production method offering functional, intricate prototypes. It also removes the requirement of post-production processing, reducing production expenses. Continuous liquid interface production (CLIP) offers fast production times and expedites prototype manufacturing timeframes.
The introduction of 3D metal printing also facilitates the creation of precise and durable prototype components. 3D printing enhances prototype workflows, allowing for savings on costs and time. Additive manufacturing processes allow for streamlining design iterations and more material options.
2 Interactive Design & Engagement in Prototyping
The scope of prototyping projects has limitations due to the software visualization platforms available to manufacturers. The rise of software-driven manufacturing systems in the last 25 years has seen many innovations in tech-inspired platforms and software built on open-source code.
This democratization of tech in the manufacturing industry allows design specialists and technical users to construct interactive production processes that drive the expected results. The introduction of AI in 2023 promises huge advancements in software applications and manufacturing processes.
3 IoT-Powered Monitoring & Simulation
Implementing IoT devices in manufacturing and prototyping processes allows access to real-time analysis, acquisition, and management data, improving decision-making for stakeholders involved in the manufacturing process.
Connected IoT devices allow manufacturers to harvest data on usage patterns, performance, and metrics that drive product design processes. For instance, they enable designers to evaluate and optimize designs before executing the prototyping process.
Manufacturers can adjust processes in real-time by tapping into the data to make instant adjustments to processes to optimize efficiency and results.
4 Sustainable Eco-Friendly Materials
The world is moving away from waste in industry, with manufacturers doing everything they can to reduce material waste. Less waste means more cost-efficiency and less environmental damage at all levels of the material supply chain.
Manufacturers lean toward using environmentally sustainable materials such as recycled plastics and bioplastics. These renewable biomass sources are compostable and biodegradable, limiting their environmental impact.
Manufacturers leverage nanotechnology like nanocellulose in medical product manufacturing to improve sustainability and help organizations reach their environmental goals.
5 Generative AI Design
As we move into a more technologically advanced society, AI (Artificial Intelligence) is the talk of the town in 2023 and 2024. AI promises many innovations in the rapid prototyping industry. AI continues to advance at breakneck speed. It won’t be long before the generative technology can perform tasks like writing CNC code.
AI systems can assist manufacturers in exploring, validating, and comparing designs simultaneously. AI algorithms leverage machine learning to forecast customer expectations and requirements. AI also offers the potential for automating many processes in rapid prototyping projects.
Manufacturers save time and costs on projects with AI, automating many production tasks to lower production expenses.
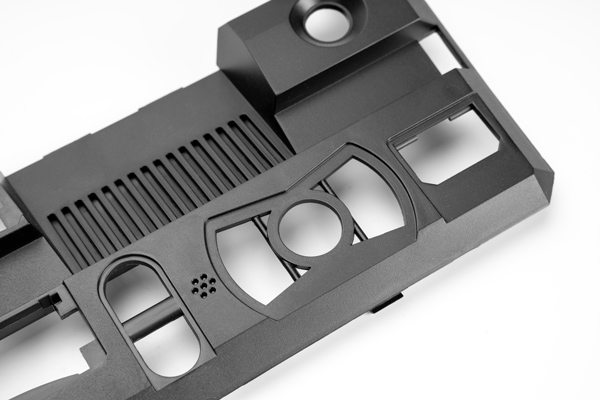
plastic injection molding part
6 Precision Manufacturing
Manufacturing isn’t 100% efficient. A significant amount of material waste is created in rapid prototyping and mass manufacturing projects. To counter this issue, manufacturers are moving towards precision injection molding processes that produce minimal waste.
Advances in injection molding technology, including insert molding, gas-assisted injection molding, and micro-injection molding, are creating waves in the manufacturing industry. For example, the use of micro-injection molding allows for the development and manufacturing of small-scale prototypes with intricate design features.
Insert molding allows for the seamless integration of components, streamlining the assembly process and improving the durability of manufactured components.
Gas-assisted injection molding enhances component quality by reducing material consumption and defects in rapid prototyping projects.
7 Multi-Technique Manufacturing Processes
We can expect 2024 to bring advancement in hybrid manufacturing technologies. The additive and subtractive prototyping technologies allow for the creation of complex components and prototypes through improvements in precision and effeminacy.
For instance, the fusion of CNC and laser-powder bed fusion allows for constructing intricate prototypes using layer-by-layer construction with excellent degrees of precision and accuracy. Hybrid milling combines 3D printing with CNC technology for high-precision rapid prototypes with improved dimensional accuracy and enhanced production speed.
8 Remote Collaboration
Cloud computing solutions allow production team members and customers to access project information and collaborate remotely. It erases geographical boundaries, promoting real-time collaboration and teamwork.
Collaborative tools allow for centralized storage of design data for easy sharing and decision-making, with fewer errors in the prototyping process. Software as a Service (SaaS) platforms allow for the optimization and improved utilization of manufacturing resources.
9 AR/VR Design Assistance
Immersive AR and VR technologies improve operational efficiency and enhance results with the prototyping design process. AR allows engineers and designers better implementation and design correction, providing a way to overlay digital representations of prototypes into real-world environments.
The result is the ability to assess performance and design features in real-time. Virtual reality offers engineers, designers, and manufacturers an immersive 3D experience that facilitates early-stage testing of prototypes.
Extended reality (XR) blends VR, AR, and mixed reality (MR) in digital spaces. The result is a more immersive and interactive user experience and improved cost efficiencies. Designers also get a collaborative platform to alter and refine designs.
10 Reverse Engineering
This practice allows design engineers to analyze the design of existing parts or products, assessing them for improvement. By comprehending and deconstructing engineered components’ functions, manufacturers can use the information to reduce production costs, improve design functionality, and improve quality standards.
Integrating this technology with AI and machine learning algorithms significantly benefits the rapid prototyping industry. The scanners accurately capture details, leveraging AI to improve data processing and accelerate the prototyping process.
The result is enhanced cost-efficiency, speed, and accuracy in prototype design and development. Engineers, designers, and manufacturers benefit from these technological advancements, accelerating product development while optimizing design and reducing the need for revisions.